Proper bunker silo management is key for high quality forage
As corn silage harvest approaches, producers should remember some principles that can be used to help optimize silage quality for their operation.
Use of an inoculant - Lactobacillus buchneri
The use of inoculants is one of the tools available for use by silage producers that has lived up to its billing saving the farmer money. When air is introduced into silage at the start of the fermentation process, there is a delay in beneficial bacteria that produce lactic acid. The longer air is allowed to infiltrate the silage, the more you can expect quality to decrease due to undesirable fermentation and a loss in nutritive value. According to Limin Kung, Jr. in “Aerobic Stability of Silage,” the aerobic spoilage during storage is responsible for the majority of total dry matter loss in forages and may be as high as 30 to 40 percent.
Lactobacillus buchneri has been used as a silage inoculant to enhance the aerobic stability of silages. When applied at the time of ensiling at the rate of up to 5 x 105 colony-forming units per gram of fresh material, L. buchneri has been demonstrated to improve aerobic stability of high moisture corn, corn silage, alfalfa silage and small grain silages relative to untreated controls.
The use of this bacterium is recommended when heating and spoilage are decreasing silage fermentation quality. Using L. buchneri has resulted in an increased concentration of acetic acid, thereby reducing the losses of nutrients and decreasing the chances for lowered animal performance.
Limit air, water and oxygen into the silage by sealing properly
When a silo is not sealed properly, air and water can infiltrate the silage and affect both the quality and quantity of silage available. Air allows yeasts and other undesirable microbes to develop. These microbes consume fiber and nutrients, reducing feed value and may also affect forage dry matter intake. Moisture additions dilute acid levels in the silage, which allows the rate of microbial growth to increase dramatically.
To alleviate the negative effects of air and water, the most common method for covering bunker silos has been the use of plastics weighted down by tires. Recently, the use of oxygen barrier film has been incorporated into the process to seal the silos. The rate of oxygen transmission through the plastic has been reported to be as low as 4 cc/m2/day compared to typical white/black plastic of 1,650 cc/m2/day.
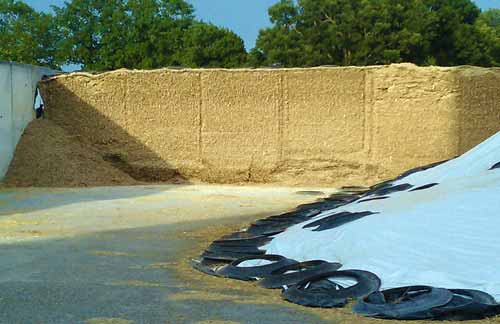
A better-managed bunk silo.
Cover the silo right away
Don’t delay the process of covering the silo since every day of delay increases the loss of dry matter in silages. Research has shown that the delay in sealing the silo with a plastic barrier resulted in 10 percent higher dry matter losses compared to silos sealed immediately after filling.
For more information, contact Michigan State University Extension educator Phil Kaatz at 810-667-0341 or kaatz@msu.edu.
References
- Aerobic Stability of Silage, Limin Kung, Jr.